Market Overview
Pads and pipelines have a vital role to play in the oil and gas industry. While wells lay the groundwork for extraction and production stages, pipeline systems facilitate shipping and transportation of oil and gas over long distances to end-users.
Experience Overview
As an engineering firm, Vista Projects has worked with numerous clients on greenfield well pad development and brownfield well pad optimization projects. Both development strategies encompass the philosophies of standardization and modularization to ensure projects are on time and on budget.
In the past ten years, Vista Projects has completed over 300,000 hours of engineering effort developing well pads and pipelines for clients.
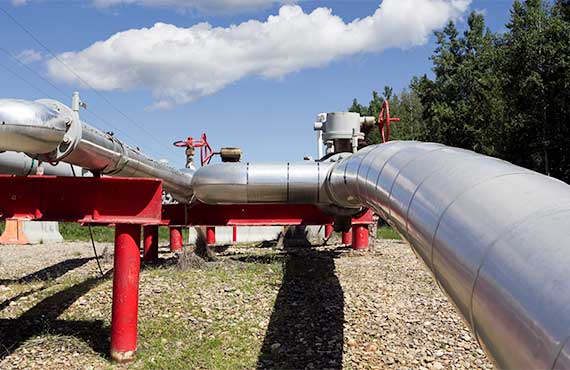
Vista Projects also has extensive experience with utilities, tankage, and well pad & pipeline development. Our project history includes long-term brownfield programs and multi-phase greenfield expansion projects.
Brownfield
Vista Projects has extensive brownfield engineering experience in the in-situ heavy oil market, including long-term programs of small-to-medium-sized sustaining capital projects leading oil and gas producers.
Typical projects range from small MOC projects up to $200M debottleneck, turnover, and steam capacity expansions.
Our proven program management methodology is streamlined, robust, and scalable, taking the risk and confusion out of program governance.
Highlighted experienced from a multi-year brownfield well pad optimization program.
- Iterative design evolution to reduce capital cost and well downtime for the conversion of gas lift to ESP and PCP based production resulted in:
- 50% reduction in production interruptions during conversion
- 20% reduction in capital cost per wellhead control module through selective design during the initial gas lift mode for re-use in ESP operation
- Well pad control module design optimization project for second-generation ESP day-one-ready modules
- Flexibility for multiple operation modes without module reconfiguration
- Re-use of gas lift and heel production piping and designing and procuring equipment for re-use
- Reduced design margins, fit-for-purpose streamlining of specification requirements, optimized instrumentation selection, and elimination of unnecessary components
- Multiphase testing technology evaluation for regulatory approval and subsequent commercial implementation
- Brownfield program success led to a greenfield conceptual design, FEED engineering for a four-well pair pilot for testing new technologies:
- Multiphase metering technology
- Solvent injection
- ESP/PCP day-zero evaluations
Greenfield
Greenfield advancements in well-pad design have focused on a templated approach that lowers costs through modularized designs that are suitable across well pads on multiple assets. Vista Projects’ efforts resulted in a 40% reduction in total installation cost (TIC) and removed months from the production schedule.
Success factors
- Utilizing a standardized bolt-together module
blocks to suit any number of well pairs, creating
a manufacturing process rather than a fabrication
process - Minimizing field construction whereby the site
work becomes essentially setting & final bolt up
of modules - Making minor pre-investment to allow future operating modes to be added at a drastically lower cost over the life cycle of the pad
- Eliminating excessive design margins
- Eliminating unnecessary pad facility buildings
- Incorporating expansion loops into modules, minimizing field-run piping
- Minimizing valve counts thru selective utilization of break-out spools, adjusting process isolation philosophies to employ well or pad shut-ins to eliminate double B&B valves
- Minimizing installed spare equipment
- Utilizing equipment for multiple services
- Minimizing instrumentation by retaining only the necessary components
- Removing costly sampling equipment and meter test facilities
Highlighted Projects
Well Pads and Pipeline Front End Engineering Design (FEED)
Vista Projects worked with its client to design the equipment and systems for a 4-pad, toe-to-heel-air-injection (THAI) in-situ heavy oil recovery project near Conklin, Alberta.
The 10,000 barrel per day project included 5 well-pairs for each of the 4 pads and an additional pad with cooling and oil/water separation and air/steam production.
Vista Projects provided comprehensive FEED services as well as project management, quality surveillance, construction management and commissioning and start-up assistance. Vista Projects also managed contractor bidding, cost control and scheduling requirements for the project.
Well Pads and Pipelines Detailed Engineering (DE)
This project involved the engineering design of pads and pipelines for a commercial-scale facility incorporating proprietary toe-to-heel air injection (THAI) technology utilized in an in-situ pilot plant. Of special interest in terms of pipeline design was the challenge of handling large volumes of sand entrained in the emulsion: Vista Projects ensured that a delicate balance was reached to keep liquid velocities low enough to avoid pipeline erosion, yet high enough to avoid sand deposition.
The project’s focus was the engineering design of four pads with five well pairs each, complete with wellhead separators. Two of the pads acted as accumulation points for oil emulsion and also accommodated other equipment, including air compressors, tanks, glycol heaters and steam generation equipment.
Aboveground pipelines connecting the new pads to the central processing facility (CPF) included a 20″ sour gas line, a 6″ sour oil emulsion line, a 6″ produced water line, a 12″ high-pressure air line, a 6″ boiler feedwater line, a 4″ fuel gas line and a 4″ recovered condensate line. An existing 3″ fuel pipeline located under one of the new pad sites required Vista Projects to reroute the existing line.
This existing pipeline was located under the new pad site, and commercial expansion plans posed a risk of long-term service interruption for the facility. In response, Vista Projects rerouted the existing pipeline away from the new pad site, enabling the facility to maintain production levels while the new steel pipeline was tied in from the connection point to the rack piping.
Pipeline & Facilities for Miscible Flood
In order to convert existing facilities and infrastructure associated with the existing waterflood to a miscible flood, the client chose Vista Projects to complete the design of a buried pipeline and ancillary facilities including 39 km of pipe, pipeline risers, new piping headers, and meter stations.
Pipe of the required specification and quantity for this project generally takes six months or more to fabricate and coat, depending on mill availability. However, the project timeline required the pipe within two to three months. In addition to time constraints as a result of a fast-approaching end to the winter muskeg construction season, pipe mills were reluctant to produce a small quantity of such specialized pipe.
Vista Projects was able to meet all of these challenges and successfully secured all the materials in a timeframe that allowed the project to proceed in accordance with the client’s schedule.
Polymer Flood Expansion
Vista Projects conducted the engineering and procurement work for a client who was expanding its polymer injection from the pilot phase to a commercial operation. The project required approximately 900 m3/day of polymer injection to nine injection wells located at 2 separate pad locations.
Major equipment for the project included polymer hydration skid, water treatment facility, various 2,000-barrel water tanks, MCC expansion, and polymer injection skid. A Fiberspar pipeline of approximately 500 metres in length was constructed to bring polymer to a five-pump injection skid at one pad site for 5 injection wells at that location. Water for the hydration process will come from source water wells. The use of produced water from one of the client’s batteries required the installation of 2 pumps at the battery location to transport water to the polymer hydration skid via 5,000 metres of new pipeline.
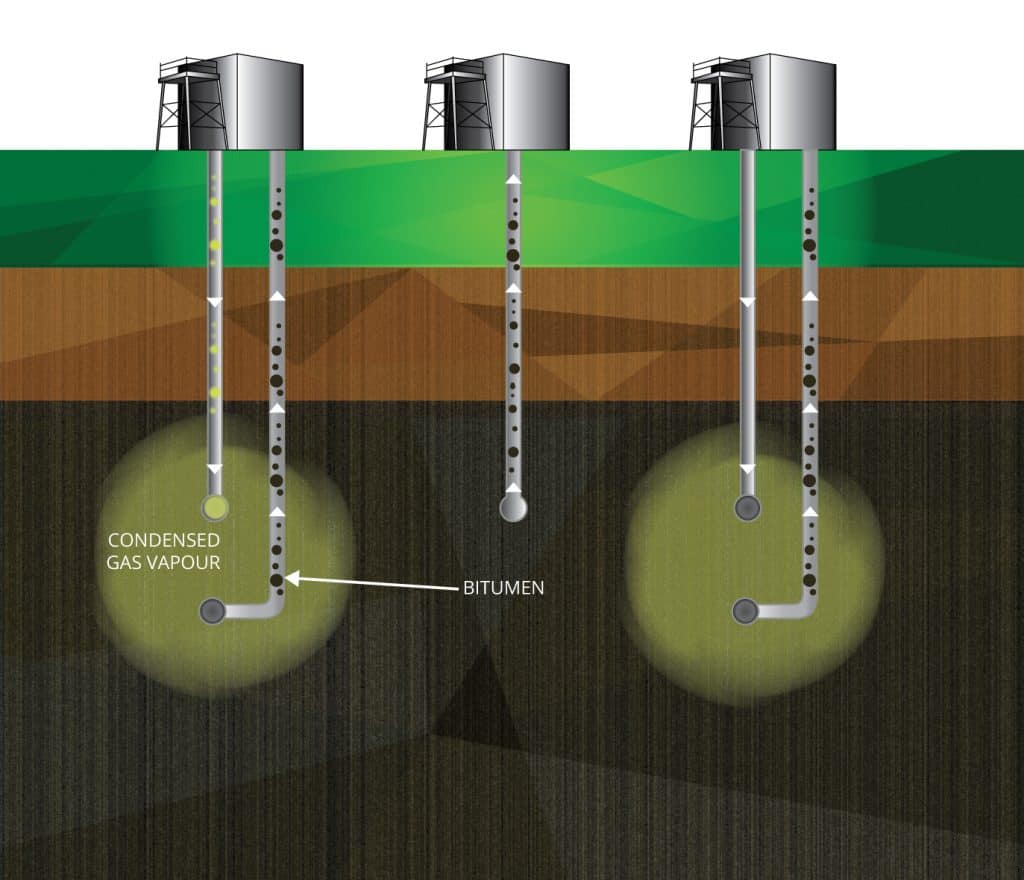
Enhanced Modified Vapour Extraction (eM-VAPEX) Recovery
Vista Projects performed the FEED and detailed engineering on a project that involved a new solvent-based in-situ recovery technology at a commercial SAGD facility. The installed technology included new facilities to process solvent for recovery and recompression. The project included 13 injector wells, which generated production from 24 existing producer wells.
Toe-To-Heel Air Injection (THAI) Detailed Engineering
The project’s focus was the engineering design of four pads with five well pairs each, complete with wellhead separators. Two of the pads acted as accumulation points for oil emulsion and also accommodated other equipment, including air compressors, tanks, glycol heaters and steam generation equipment.
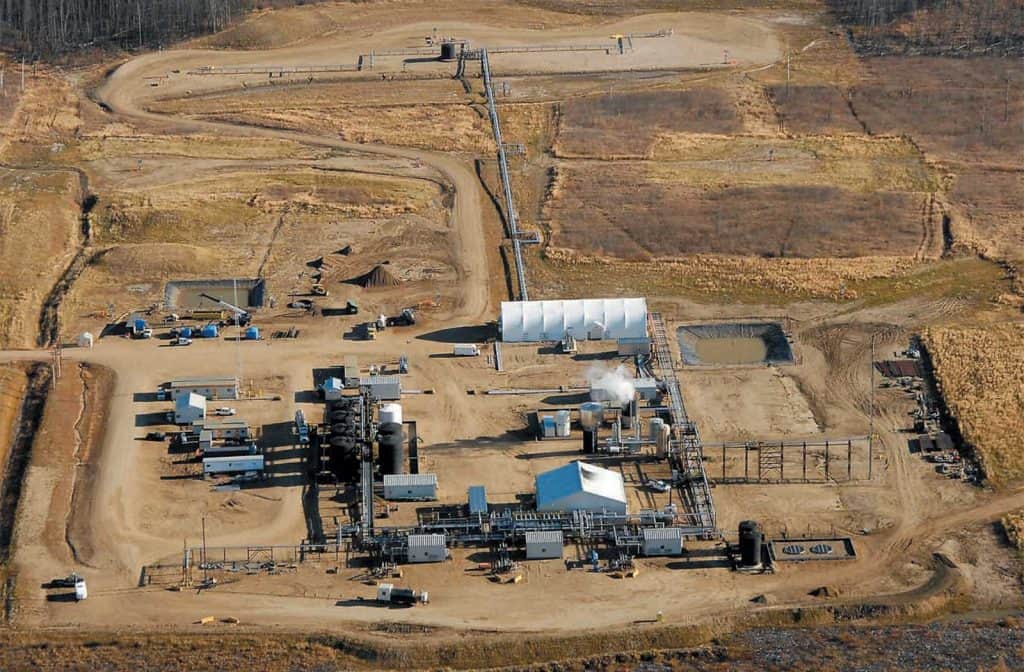
Related Brochures
Looking for more information? Download one of our related brochures to learn more about Vista’s engineering consulting services.
Project Experience Overview
Well Pad Experience
Engineering Capabilities
Vista Projects has a broad range of engineering services experience with well-pad and pipeline projects. Our work includes the first-ever use of a Multiphase Flow Meter (MPFM) for the Alberta Energy Regulator (AER), well-pad testing, artificial lift, and solvent injection, as well as other innovative solutions for well-pad conversion projects.
Vista Projects understands the importance of designing these systems with requisite equipment to ensure better output and efficiency to clients.
Design Templates
Vista Projects works with clients closely to offer fit-for-purpose pipeline and well-pad facility designs. We work with clients to develop templated designs that offer construction and operational efficiency.
Solvent Injection
Solvent injection is one of the most viable heavy-oil recovery methods used in the oil and gas industry. It enhances the oil production rate by significantly reducing oil viscosity. Vista Projects is experienced at developing fit-for-purpose engineering designs for solvent injection pads.
Progressive Cavity Pumps (PCPs)
A type of positive displacement pump, Progressive Cavity Pumps (PCPs), or screw pumps, are used to pump viscous materials and have major applications within the oil and gas industry. They are used for providing artificial lifting solutions, worldwide.
Electric Submersible Pump (ESP)
An Electric Submersible Pump (ESP) is another artificial lift method used for pumping liquids out of wellbores. The process consists of:
- Seal-chamber section
- Surface controls
- Multi-staged centrifugal pump
- Power cable
- Three-phase induction motor
Multiphase Flow Meters
Multiphase flow meters are used for measuring the flow rates of gas, oil, or formation water in pipelines. This information helps facilitate optimization and effective control of oil fields.
Electric Submersible Pump (ESP)
Variable Frequency Drives (VFDs), or AC drives, have various applications for pipeline pumping. A type of motor controller, a VFD is mainly used in the pipeline industry to save energy and facilitate better pressure or flow.
What Our Clients Say
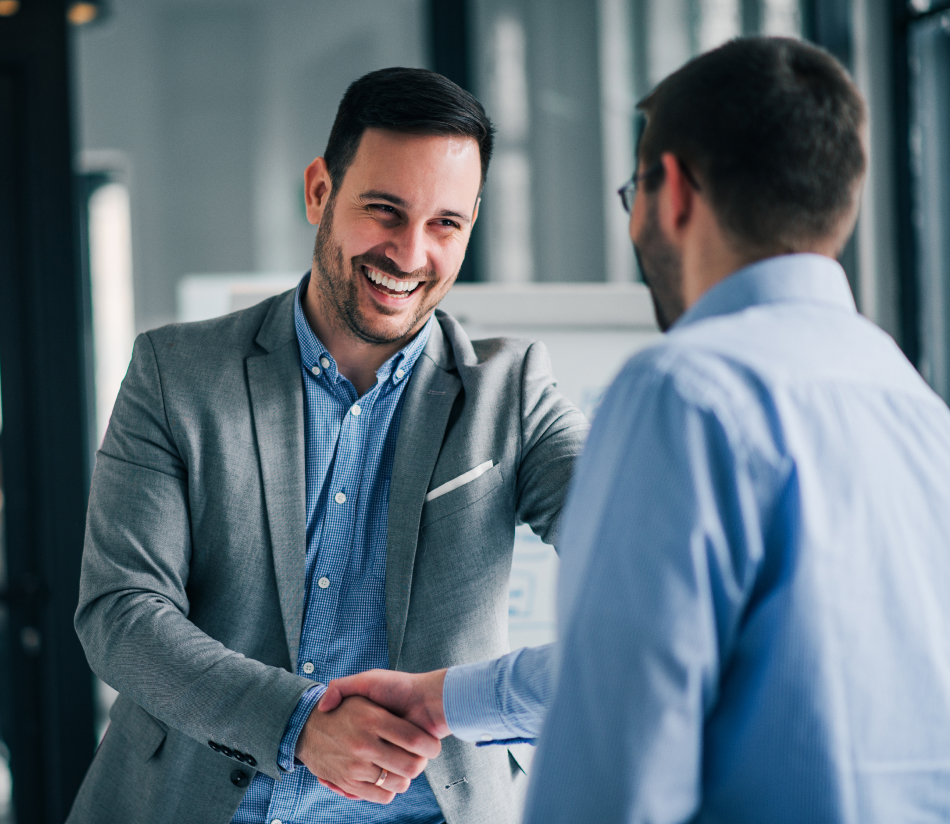
Improve your project success with the help of seasoned experts
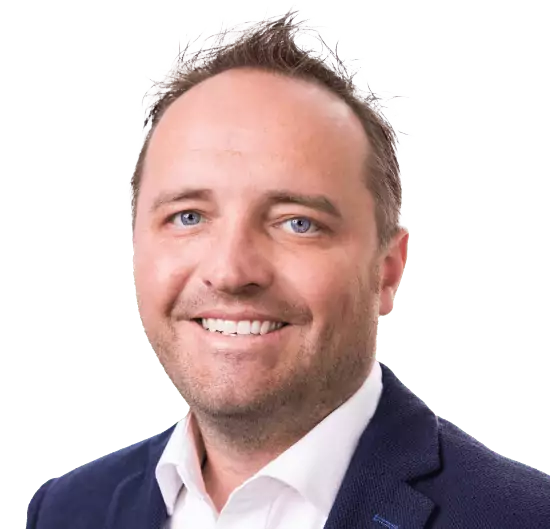
Tyler Elchuk
Business Development Director
All Clients Deserve
A Single Source of Truth
Our unique truth-based industrial engineering execution model facilitates:
- Transparency about projects and assets
- A collaborative problem-solving approach
- High-quality engineering designs
By structuring data in a single-source-of-truth (SSOT) environment, we simplify the digital transformation of your asset and help you make more informed decisions. Learn more about our system integration services.