Market Overview
Conventional heavy oil pertains to oil that can be extracted using traditional methods of drilling, compression, and pumping. Contrary to unconventional oil, conventional crude is less complex to extract. Its extraction process primarily consists of four phases:
- Exploration
- Drilling
- Pumping
- Abandoning
Conventional oil lies at the forefront of numerous industries and its increasing demand warrants the creation of facilities that need end-to-end, cost-effective engineering solutions. Vista Projects leverages its expertise in designing fit-for-purpose engineering solutions for conventional heavy oil facilities to help clients meet their challenges.
Experience Overview
Vista Projects has extensive engineering design experience with grassroots conventional heavy oil facilities. Our capabilities include the development of:
- conventional heavy oil batteries
- terminal tank farms
- pressure treaters
- satellite and gathering systems
- utilities and off-sites
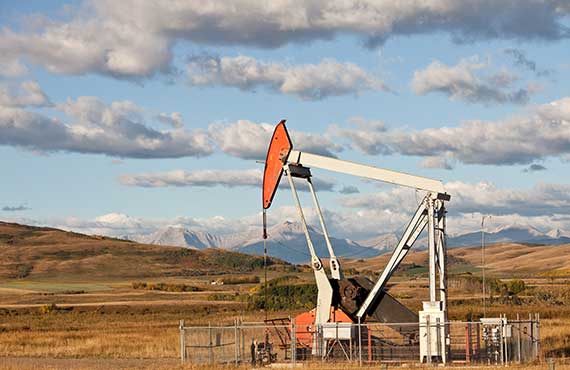
Vista Projects also has extensive experience with utilities, tankage, and well pad & pipeline development. Our project history includes long-term brownfield programs and multi-phase greenfield expansion projects.
Highlighted Projects
Battery, Field Development, FWKO
As part of a long-term partnership with this client, Vista Projects completed the detailed engineering design and procurement of a $3.5 million grassroots heavy oil treating battery processing 2,700-4,000 barrels of oil per day (BPD) or 430 – 635 m3/day of 15 API oil, featuring:
- Production manifold and test treated
- Direct fired treater with desand system
- Inlet emulsion/sales oil exchanger and sales oil tankage with pipeline tie-in
- Produced water skimming, filtration and water reinjection pumping facilities
- Desand and recycle tankage and associated pumps
- Utility systems: glycol heating system serving both process and utility requirements, instrument air, fuel gas and flare
Vista Projects also completed the detailed engineering design and procurement for the battery’s free-water knock-out (FWKO), test treater, and production satellite. The project was needed for this heavy oil battery expansion to handle 5,000 BPD or 800 m3/d of oil and 20,000 BPD or 3,200 m3/day of water, featuring:
- Direct fired FWKO vessel with desand system
- Direct fired test treater sized for 60 m3/d oil and 150 m3/d water
- Produced gas cooler
- Inlet manifold extension
- Remote satellite manifold
Oil Batteries
As part of a long-term partnership with this client, Vista Projects completed the detailed engineering design of a grassroots heavy oil treating battery processing 4,000 barrels of oil per day (BPD) or 635 m3/day of 15 API oil, featuring:
- Production manifold
- Two test treaters
- Direct fired treater with desand system
- Inlet emulsion/sales oil exchanger and sales oil tankage with truck loading
- Produced water cooling, skimming, filtration, and water reinjection pumping
- Desand and recycle tankage and associated pumps
- Glycol heating system serving both process and utility requirements
- Onsite generation of electrical power (480v, 3ph, 60hz)
- Fuel and flare utility systems
Vista Projects was also engaged to complete detailed engineering design and procurement of multiple battery expansions to this facility including the addition of:
- a pressurized FWKO to increase water handling capacity to 10,000 BPD or 1,590 m3/day, as well as a produced gas dehydration system and an instrument air package;
- a second 6,000 BPD or 950 m3/day water disposal pump with filter and booster pump, as well as a second oil emulsion inlet manifold
Vista Projects completed the detailed engineering design for a grassroots heavy oil treating battery processing up to 1,900 BPD (300 m3/day) of 18 API oil, featuring:
- Production manifold with pig receiver
- Indirect fired test heater and test separator
- Direct fired treater with chemical injection
- Sales oil storage tankage with pipeline tie-in
- Produced water skimming, filtration, and water injection pumping facilities handling 600 m3/day
- Recycle tankage and pumps
- Sour produced gas compression (40 103 m3/day)
- Utility systems: glycol heating system, instrument air, fuel gas and flare
Low BTU Gas Combustion Study
In order to optimize the steam generation and fuel and power usage at a client’s in-situ toe-to-heel air injection (THAI) project, Vista Projects undertook a study to evaluate the potential for combustion of low-BTU gas in the project’s on-site turbine.
The project was completed on time and on budget between February and July 2009.
Pipeline and Emulsion Tank
Vista Projects performed the detailed engineering design for a client planning to drill additional production wells at an existing conventional oil battery. Vista Projects was contracted to design the emulsion tanks and related gas and fluid treatment and handling processes, as well as the piping from the production wellhead to the on-site tank farm.
The project was designed to meet the client capacity specifications of 300 m3/day of sour oil production as well as produced gas. The test and production tanks required 4-day production storage capacity.
Heavy Oil Battery and Steam Facility Expansion
As part of a long-term relationship with this client, Vista Projects completed engineering studies, pre-FEED, FEED and detailed engineering design for a grassroots oil treating battery initially processing 3,000 barrels of oil per day (BPD) or 412 m3/day.
Vista Projects was also engaged to perform subsequent expansion work to increase the production rate to 15,000 BDP or 2,060 m3/day. Features included:
- Production manifold and test tank
- FWKO and direct fired treaters with desand systems
- Inlet emulsion/sales oil exchanger, sales oil cooler, produced water cooler
- Coalescing tank and sales oil storage tanks with future pipeline tie-in
- Produced water skimming, filtration and water reinjection pumping facilities
- Desand and recycle tankage and associated pumps
- Utility systems: glycol heating system (process & utility) glycol cooling system for produced gas cooling, instrument air, fuel gas, and flare
- Steam expansion – grassroots thermal steam generation facility with water treatment system, three 50 MM BTU/hr steamers, steam distribution system to 15 wells, and thermal production gathering system complete with manifold and test separator
Related Brochures
Looking for more information? Download one of our related brochures to learn more about Vista Projects’ engineering consulting services.
Project Experience Overview
Modularization Optimization
Engineering Capabilities
As an engineering consulting firm, our conventional heavy oil engineering capabilities include the development of oil batteries, tank farms, satellites, and gathering systems, as well as utilities and offsites.. We have also provided detailed engineering studies on conventional oil extraction and handling processes and optimization.
Battery and Satellite Development
Oil batteries are groups of tanks interconnected to receive oil from wells. They remove water from the oil and treat the oil to decrease viscosity before it’s pumped into pipelines. Vista Projects has extensive technical expertise in developing conventional oil batteries and satellites, with a particular focus on upgrading and debottlenecking projects.
Equipment Selection and Procurement
To decrease operating costs for conventional oil facilities, proper strategies are required for the process of selecting and procuring equipment, goods, materials, and services. Vista Projects’ data-centric approach to project execution is critical to the development of cost-effective procurement strategies.
Water Treatment and Desanding
Oil and gas facilities can generate large volumes of produced water containing organic and chemical compounds. This makes produced water treatment and management integral to the operation of conventional and heavy oil facilities. Deoiling and desanding equipment is used to remove oil and solids, which purifies and improves produced water quality, making it suitable for re-use in the facility.
Utilities and Offsites (U&O)
Utility and offsite support facilities are important components of any well-designed conventional oil plant. Typical U&O systems contain:
- Utilities: Cooling Water, Air and Water Systems, Steam and Power Generation, Natural Gas, Heat Medium, and Nitrogen
- Offsites: Wastewater Treatment/Disposal, Firewater System, Loading, and Unloading, Metering/Custody Transfer
Tankage, Infrastructure, and Processing Facilities
Crucial aspects of oil processing, tankage systems are key to sustaining the long-term profitability of conventional oil facilities. While some tanks are used to store oil generated by a well, other tanks serve waste management functions.
What Our Clients Say
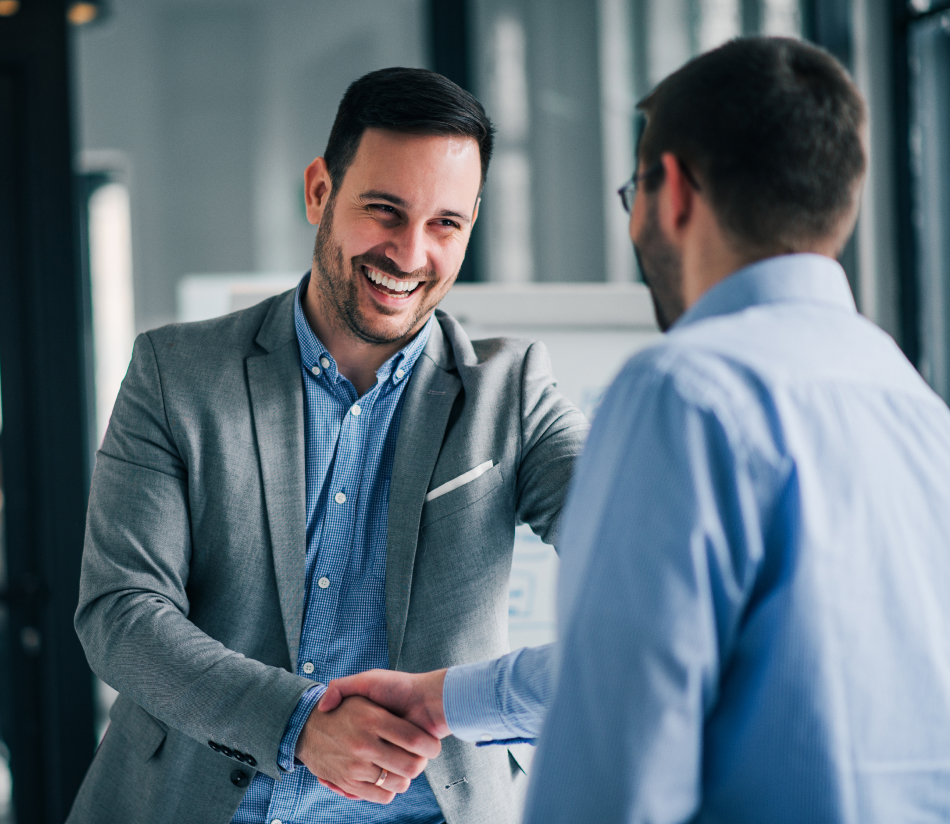
Improve your project success with the help of seasoned experts
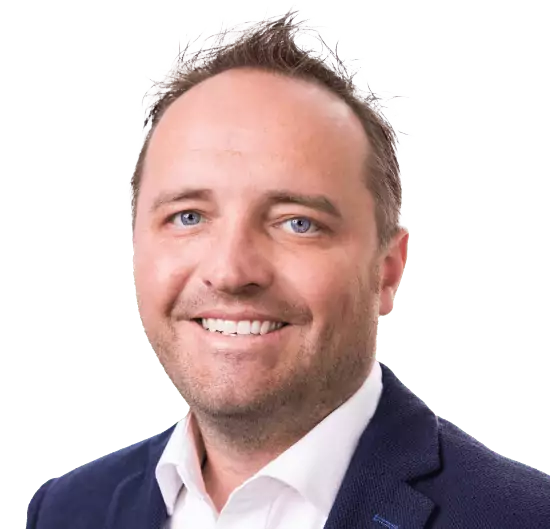
Tyler Elchuk
Business Development Director
All Clients Deserve
A Single Source of Truth
Our unique truth-based industrial engineering execution model facilitates:
- Transparency about projects and assets
- A collaborative problem-solving approach
- High-quality engineering designs
By structuring data in a single-source-of-truth (SSOT) environment, we simplify the digital transformation of your asset and help you make more informed decisions. Learn more about our system integration services.