This post is for anyone who has ever wondered what is a cogeneration plant or how one works.
Also known as combined heat and power (CHP), the term cogeneration describes the simultaneous generation of electrical energy and usable heat from a single primary energy source, often natural gas or biofuels.
Several cogeneration system definitions exist, but overall, the term applies when a single fuel source produces two or more forms of energy. Cogeneration is also sometimes called recycled energy.
What Is a Cogeneration Plant?
A cogeneration plant, also known as combined heat and power (CHP), is a system that simultaneously generates electrical energy and usable heat from a single primary energy source, such as natural gas or biofuels. By capturing and repurposing the heat produced during electricity generation, cogeneration plants significantly increase energy efficiency, reduce operational costs, and lower greenhouse gas emissions. This sustainable solution minimizes fuel consumption, saves money, and promotes environmental sustainability.
At the most basic level, a typical cogeneration plant has an electricity generator and a heat-recovery system.
Here are some basic elements of a CHP setup:
- Prime movers: Converts fuel into heat and electrical energy that can be used to generate mechanical energy. Examples of prime movers include gas turbines and reciprocating engines
- Electrical generator: Converts mechanical energy into electrical energy
- Heat recovery system: Captures heat from the prime mover
- Heat exchanger: Makes sure that the captured heat is put to use
What Fuels Are Used in Cogeneration Plants?
A variety of fuels can be used in cogeneration plants, including:
- natural gas
- diesel
- gasoline
- coal
- biofuels
The use of biofuels in cogeneration typically includes renewable resources, like waste gases from landfills and solid waste from agriculture.
Two broad types of CHP systems
- Topping cycle plants: A topping cycle system starts with electricity generation
- Bottoming cycle plants: Generating heat is first — waste heat produces steam that is then used to generate electricity
Bottoming cycle plants are found in industries that use very high-temperature furnaces. They’re less common than topping cycle plants in part because it’s easier to sell excess electricity.
How Does a Cogeneration Plant Work?
When a power plant generates electricity, it produces heat. If the plant releases that heat into the environment as exhaust, it represents a huge waste of energy. Most of that heat can be captured and used for other purposes. When that repurposing of heat occurs, the power plant is working as a cogeneration system.
The cogeneration process can increase overall energy efficiency, with typical systems ranging from 65 to 90 percent. Businesses that use cogeneration can lower operational costs and boost their self-sufficiency while reducing greenhouse gas emissions and pollutants.
The Story Behind CHP
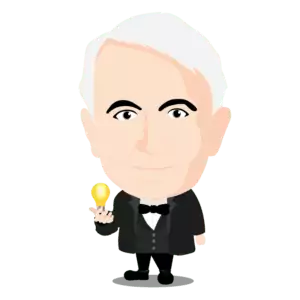
The concept of combined heat and power isn’t new. Europe and the U.S. both used forms of CHP as early as 1880 to 1890. During those years, many industries used their own coal-operated power plants to generate the electricity that powered their mills, factories, or mines.
The steam that was produced as a byproduct was used as thermal energy for various industrial processes or to heat the space.
Thomas Edison designed and built the first commercial power plant in the U.S. in 1882 and it just so happened to be a cogeneration plant. The thermal byproduct of Edison’s Pearl Street Station in New York was distributed as steam to local manufacturers and it also heated nearby buildings.
The Rise and Fall of CHP Use
In the early 1900s, CHP systems produced about 58 percent of the total on-site electrical power generated in industrial plants in the U.S. That percentage plummeted to only 5 percent by 1974, according to “Cogeneration: Technologies, Optimization, and Implementation“, edited by Christos A. Frangopoulos.
There were many reasons for that sharp decline.
Electricity from central power grids became more reliable and cheaper to buy and fuel, like natural gas, became available at a low cost, making privately owned coal-fired on-site power plants less desirable. Also, the government increased the number and reach of the regulations and restrictions concerning electricity generation.
However, when fuel costs skyrocketed in 1973 and awareness of the harmful effects of pollution grew, cogeneration became highly relevant again.
Why Use Cogeneration?
There are several benefits to using cogeneration. The main reasons to use CHP are to save energy and costs by reducing fuel consumption. For instance, in the U.K., existing users of CHP save 20 percent of their energy costs.
With CHP, when fuel energy is converted into mechanical or electrical energy, the bulk of the heat that’s released isn’t wasted. Less fuel is needed to generate the same amount of useful work that a conventional power plant would produce.
That reduced fuel use has several benefits, including:
- Lower fuel costs
- Reduced fuel storage and transportation needs
- Reduced emissions – CHP is one of the most cost-effective ways to reduce carbon emissions
- Less wear on machinery due to reduced pollutant exposure
Another benefit is security.
Cogeneration is considered a secure power supply since it provides stand-alone power that isn’t dependent on a municipal power grid. A business that uses cogeneration can operate off-grid or easily supplement to meet a surge in power demands.
Vista’s cogeneration engineering experience ranges from “micro” cogeneration designs that can generate between 5-10 MW of power to much larger cogeneration facilities.
Who Can Use Cogeneration?
The industrial sector has a massive need for heat and electricity. Some industries primarily use heat, like metal manufacturers, while some use mostly electricity. Other industries require both heat and electricity in varying ratios.
Each scenario can benefit from a recycled energy system. A factory that requires more electricity than heat can sell the heat to a utility and excess electricity can similarly be sold.
Cogeneration plants have three size categories:
- Small: Many small CHP plants in the U.S. and Canada are operated by the military, universities, and non-utility companies. What they share are high demands for energy use, as well as a compelling need for reliable and self-sufficient sources of energy. A Scientific American article cites a computer-networking company that saves around US $300,000 a year in energy costs due to its CHP use.
- Medium: The market is growing for medium-scale cogeneration systems. Medium-scale is defined as units that generate from 50 to 500 kW of power, according to “Cogeneration: A User’s Guide“, by David Flin. Sectors that require high loads of heat and energy, like hospitals and hotels, fall into this category.
- Large: Large CHP plants exist in energy-intensive fields, like oil refineries and food-processing facilities. These can output 500 kW or more in energy.
Vista Projects has extensive experience designing and optimizing combined heat and power systems across various industries and sectors.
When the right conditions apply, it makes sense to use cogeneration. It’s a reliable and efficient way to provide on-site power that’s beneficial economically and environmentally.