Navigating the intricate world of Instrumentation & Control Engineering can be quite the endeavour, especially when gearing up for an interview. Whether you’re a fresh graduate or a seasoned professional, understanding what questions might come your way is crucial in preparing for success. This article delves into the common interview questions that Instrumentation & Control Engineers might face.
From technical knowledge and problem-solving skills, to experience with specific projects and an understanding of regulatory standards, we’ve got you covered. Additionally, we explore the basic principles of process control, the significance of PID control, and the role of SCADA in industrial automation, among other topics.
Whether you’re brushing up on the basics or looking to deepen your understanding of the latest trends in the field, this guide equips you with the knowledge and confidence you need to ace that interview.
What are Common Interview Questions for an Instrumentation & Control Engineer?
Interviews for an Instrumentation & Control Engineer position are designed to evaluate a candidate’s technical acumen, problem-solving capabilities, and comprehensive understanding of both control systems and instrumentation. Below is an overview of the typical questions you might face, categorized for clarity:
- Technical Knowledge and Skills: This category probes your foundational and advanced knowledge of instrumentation and control engineering. Questions such as, “Can you explain the working principle of a PID controller?” or “How do you calibrate a pressure transmitter?” test your grasp of essential concepts and practical application skills.
- Problem-Solving and Analytical Skills: You may face hypothetical scenarios requiring solutions, such as troubleshooting a malfunctioning control loop or designing a system with specific parameters; for example, “How would you approach diagnosing a recurrent problem in a flow measurement system?” These questions assess your analytical prowess and problem-solving methodology.
- Experience and Projects: Interviewers delve into your experience and the projects you’ve spearheaded. Questions like, “Can you describe a challenging project you worked on and how you overcame the obstacles?” aim to unearth insights into your hands-on experience, project management capabilities, and teamwork dynamics.
- Regulatory and Safety Knowledge: The critical importance of safety and compliance in this field prompts questions related to industry standards and safety protocols, such as “How do you ensure compliance with ISA standards in your designs?” This evaluates your commitment to and knowledge of safety and regulatory mandates.
- Soft Skills and Cultural Fit: To gauge how well you may fit into the team and company culture, you may be asked questions like “How do you handle tight deadlines or work under pressure?” or “Can you give an example of how you’ve worked effectively in a team?“. These inquiries are crucial for assessing communication skills, teamwork aptitude, and stress management strategies.
Preparing for these common questions can significantly bolster your likelihood of success in landing a position as an Instrumentation & Control Engineer. A solid understanding of the underlying principles, the ability to effectively articulate past experiences, and showcasing a problem-solving mindset are pivotal strategies for acing the interview.
Explain the Basic Principles of Process Control
Process control is essential in optimizing the performance of industrial systems to ensure efficiency, reliability, and safety. It involves the regulation of variables such as temperature, pressure, flow, and level to maintain optimal process conditions.
This strategy offers a complementary approach to feedback control, providing a comprehensive method for process regulation. Together, these principles underpin modern process control systems, enabling the precise management of industrial operations through sophisticated control strategies. Mastery of these principles allows for the design and implementation of efficient, responsive, and safe control systems across various industrial applications.
PID Control: Proportional, Integral, Derivative Elements
PID control is a cornerstone in optimizing industrial processes. It involves adjusting system outputs to minimize the discrepancy between a desired setpoint and the actual process variable. It integrates three pivotal elements:
- Proportional (P): This component generates an output directly proportional to the current error value, playing a crucial role in rapidly reducing the error and enhancing the system’s responsiveness.
- Integral (I): Focused on the accumulation of past errors, it provides a corrective action derived from the sum of error over time, effectively eliminating the residual steady-state error that eludes the grasp of proportional control.
- Derivative (D): By evaluating the rate of error change, it anticipates future errors, contributing to the system’s stability by mitigating overshooting and ensuring a smoother convergence to the setpoint.
Feedback vs. Feedforward Control: Definitions and Applications
Feedback and feedforward control mechanisms embody two strategic approaches in process control systems, each designed to maintain desired operational conditions amidst disturbances.
- Feedback Control: Emblematic of a reactive strategy, this method measures the output of a process, juxtaposes it with the desired setpoint, and implements corrections to mitigate any deviations. Its universal application across a myriad of industrial settings underscores its simplicity and efficacy, particularly in scenarios where output measurement and subsequent adjustments are feasible to maintain control.
- Feedforward Control: In contrast, feedforward control adopts a proactive stance, anticipating process disturbances prior to their impact on the system. By adjusting process inputs based on disturbance measurements, it aims to pre-empt deviation. This method shines in environments where disturbances can be detected and corrected before they influence the process outcome, offering a pre-emptive shield against potential disruptions.
Incorporating both feedback and feedforward control within industrial control systems furnishes a dual-layered defence against variability, enhancing the robustness, efficiency, and adaptability of process control methodologies.
What is a PLC and How Does it Work?
A Programmable Logic Controller (PLC) is a computer utilized in the automation of electromechanical processes across a wide range of industries, including manufacturing, power generation, and food processing.
PLCs enable engineers and technicians without deep programming expertise to effectively manipulate and implement complex control strategies. The combination of robustness, adaptability, and user-friendly programming has cemented the PLC’s role as a cornerstone of modern industrial automation.
Programmable Logic Controller: Core Functionalities
A Programmable Logic Controller (PLC) is an industrial computer designed to automate control tasks across various applications. Its core functionalities are pivotal for its integration and performance in industrial settings:
- Real-Time Operation: Central to their utility, PLCs offer real-time processing capabilities, ensuring inputs are quickly translated into necessary outputs without delay, which is critical for process continuity and safety.
- Modularity: The modular design of PLCs allows for easy customization and scalability. This means users can add or remove input/output (I/O) modules, communication modules, and specialized function modules to meet the specific needs of their processes.
- Robustness: Built to withstand the rigours of industrial environments, PLCs are resilient against vibration, extreme temperatures, and electrical noise, guaranteeing consistent and reliable operation under challenging conditions.
- User Programmability: PLCs feature user-friendly programming interfaces, enabling the creation, modification, and troubleshooting of control programs that cater to unique process requirements.
Ladder Logic: Basics and Programming Examples
Ladder logic is a graphical programming language that simplifies the process of coding for PLCs by emulating electrical relay diagrams. Its straightforward and intuitive structure makes it an ideal choice for Instrumentation and Control Engineers and technicians.
- Basics: Constructed with rungs, ladder logic diagrams represent control logic operations where each rung corresponds to a specific action controlled by the PLC. Symbols are used to represent inputs and outputs, mirroring the components of relay logic circuits. The execution flow of ladder logic is from left to right and top to bottom, similar to how electrical schematics are organized.
- Programming Examples:
- Start/Stop Circuit: A classic use case involves creating a circuit that allows a motor to start or stop. This is achieved by using a normally open (NO) start button to activate a relay coil. Once energized, the relay maintains the circuit closed, even after releasing the start button, through a hold-in contact. A normally closed (NC) stop button is used to break the circuit and stop the motor.
- Motor Control with Interlock: For scenarios requiring the operation of two motors but ensuring only one operates at any given time, ladder logic can implement an interlock function. This is done by programming the PLC so that activating the relay for one motor automatically cuts off power to the other motor’s relay, preventing simultaneous operation.
Through these examples, ladder logic demonstrates its effectiveness and adaptability in addressing a wide array of control logic scenarios, underscoring its value in the realm of PLC programming.
Describe the Significance of 4-20 mA Signals in Instrumentation
The 4-20 mA signal standard stands as a pivotal element in the realm of industrial automation and control systems, celebrated for its straightforwardness and resilience. This current loop standard is universally acclaimed for its capability to convey analog signals across distances while maintaining signal integrity. The essence of 4-20 mA signals is their ability to preserve signal accuracy and reliability amid the electrical noise prevalent in industrial settings.
The selection of the 4 mA to 20 mA range is strategic; 4 mA signifies the signal’s baseline (zero level), distinguishing itself from actual zero current. This distinction ensures that any current detected between 0 mA and 4 mA can signal a fault, such as a wire break, thereby bolstering the safety and diagnostic capabilities of control systems. The peak of 20 mA corresponds to the maximum measure of the parameter in question, offering an expansive dynamic range for meticulous monitoring and control.
A paramount advantage of the 4-20 mA signals is their inherent noise immunity. By favouring the transmission of current over voltage, the susceptibility to voltage drops and electromagnetic interference is markedly reduced, safeguarding signal integrity across extensive cable lengths. This attribute renders the 4-20 mA standard exceedingly apt for industrial applications where signal cabling may traverse expansive distances or areas laden with high electrical noise.
Moreover, the 4-20 mA signal standard streamlines the integration of a multitude of sensors and actuators into a cohesive control system. Devices can be loop-powered, deriving their operational power directly from the 4-20 mA signal, which mitigates wiring complexity and diminishes power supply demands. In essence, the prominence of 4-20 mA signals in instrumentation is rooted in their reliability, noise immunity, and diagnostic prowess, rendering them an indispensable component in the architecture and functionality of contemporary industrial control systems.
Standard for Analog Signal Transmission
The 4-20 mA current loop is the industry standard for analog signal transmission, particularly within industrial automation. Its widespread acceptance is attributed to the critical need for a dependable and uncomplicated method for transmitting data from sensors and actuators across considerable distances. This standard capitalizes on a straightforward yet effective principle: the current flowing through the loop is directly proportional to the value of the physical parameter being monitored, such as temperature, pressure, or flow rate.
Opting for current as the medium for signal transmission significantly reduces the potential for signal loss due to cable resistance, thereby safeguarding the fidelity of the transmitted data.
Advantages: Noise Immunity and Simplicity
Among the key benefits of the 4-20 mA standard, noise immunity and simplicity stand out as pivotal:
- Noise Immunity: The industrial landscape is replete with electrical noise, a pervasive challenge that can distort signal transmission. The 4-20 mA signal, by its inherent nature as a current-based transmission method, exhibits a remarkable resistance to such interference. This quality ensures that the integrity of the signal is maintained across distances, rendering it exceptionally suited for use in environments dominated by electrical noise.
- Simplicity: Embracing the 4-20 mA standard streamlines the architecture and deployment of control systems. Compatibility and integration of devices following this standard are straightforward, eliminating the need for intricate conversion or compatibility protocols. Moreover, the linear correlation between the signal and the measured parameter facilitates an intuitive and efficient analysis of the transmitted information.
These characteristics solidify the 4-20 mA standard’s role as an indispensable framework within contemporary industrial control systems, offering a reliable and efficient communication channel among the system’s various elements.
How do You Implement Safety Measures in Control Systems?
Implementing safety measures in control systems is crucial for the protection of human operators and machinery in industrial settings. It involves a systematic approach that starts with a comprehensive risk assessment to pinpoint potential hazards and assess their impact.
This regimen is complemented by staying updated on technological advancements and regulatory changes, which may necessitate updates or enhancements to the system. In summary, the implementation of safety measures in control systems demands a diligent, forward-thinking approach to risk management, utilizing cutting-edge technology and best practices to safeguard personnel and assets in complex industrial environments.
Safety Integrity Level (SIL): Criteria for Classification
Safety Integrity Level (SIL) is a metric fundamental to determining the necessary safety performance of control systems aimed at effectively mitigating risks. The classification into four distinct SIL levels, from SIL 1 to SIL 4, hinges on a comprehensive evaluation of several pivotal criteria:
- The severity of potential hazards.
- The frequency of exposure to such hazards.
- The possibility of hazard avoidance.
- The probability of failure on demand.
SIL 1 denotes a relatively lower level of risk reduction, while SIL 4 signifies the utmost level of safety integrity, where the risk potential is exceptionally high. This stratification aids in tailoring the design and execution of safety functions to align with the specific risk profile of a system.
Emergency Shutdown Systems (ESD): Key Components and Operation
Emergency Shutdown Systems (ESD) play a critical role in safeguarding industrial processes by either bringing them to a safe operational state or initiating a complete shutdown during emergencies. The efficacy of an ESD system is underpinned by its core components:
- Sensors: Front-line elements that detect abnormal or hazardous conditions, transmitting signals indicative of such anomalies to the logic solver.
- Logic Solvers: Acting as the decision-making hub, they evaluate inputs from sensors against predefined criteria to ascertain the appropriate course of action.
- Actuators: The executors that implement the directives issued by the logic solver to adjust or halt the process, thereby mitigating the risk of harm.
The operational paradigm of an ESD system is characterized by its prompt and reliable response to emergent threats, thereby minimizing the risk exposure of personnel, equipment, and the environment. The architecture and operational protocols of ESD systems are meticulously crafted to meet the SIL specifications of the processes they oversee, guaranteeing a congruent and effective level of safety performance.
Discuss the Role of SCADA in Industrial Automation
Supervisory Control and Data Acquisition (SCADA) systems are indispensable in the landscape of industrial automation, acting as the vital backbone for monitoring and controlling industrial processes and operations. These systems excel in collecting real-time data from a multitude of sensors and pieces of equipment dispersed across extensive geographical locales, synthesizing this information into a digestible and actionable format for operators and decision-makers. At the heart of SCADA functionality are four key pillars: data acquisition, network data communication, data presentation, and control.
These elements enable SCADA systems to amass large volumes of data from remote sensors, process and analyze this data, and leverage it to oversee and fine-tune the workings of machinery and processes dynamically. This capability grants an unmatched level of management and oversight over complex industrial environments, driving improvements in efficiency, reliability, and safety. SCADA systems find their application across a diverse range of industries, such as water treatment, electric power, oil and gas, and manufacturing.
Supervisory Control And Data Acquisition: Core Features
Supervisory Control And Data Acquisition (SCADA) systems significantly elevate operational efficiencies and safety standards. Their core components encompass:
- Real-Time Data Collection: SCADA systems are adept at harvesting data from a myriad of sensors and instruments, facilitating informed and timely decision-making processes.
- Process Control: They allow operators to remotely manipulate industrial processes, adjusting operational parameters in real-time based on the data received.
- Event Logging: SCADA systems record events and operational data and can generate comprehensive logs that serve as critical resources for troubleshooting and historical analyses.
- Alarming: These systems can promptly alert operators about critical conditions demanding immediate attention, thereby enabling quick responses to avert potential issues.
- Graphical User Interfaces (GUIs): SCADA systems provide users with intuitive visual representations of process data and controls, markedly simplifying the complexities of monitoring and operational tasks.
Real-Time Monitoring and Control: Examples in Various Industries
The prowess of SCADA systems in real-time monitoring and control is exemplified across a wide array of industries, showcasing their adaptability and transformative impact:
- Water and Wastewater Management: SCADA systems are instrumental in managing the distribution of potable water and the processing of wastewater. They monitor critical parameters such as pump station activity, reservoir levels, and treatment plant operations to safeguard water quality and ensure consistent supply.
- Electric Power: SCADA systems manage the intricacies of power generation, distribution, and grid load balancing. They ensure the stability and efficiency of the power grid by monitoring substations and conducting real-time power line analysis.
- Oil and Gas: SCADA systems optimize pipeline operations, oversee remote drilling activities, and monitor oil and gas storage conditions, thereby enhancing production efficiency and ensuring operational safety.
- Manufacturing: SCADA systems streamline manufacturing processes, from managing assembly lines to automating robotic functions. They increase throughput and facilitate early detection of production anomalies.
- Transportation: SCADA systems enhance transportation safety and efficiency by monitoring traffic flows, controlling railway signals, and managing critical infrastructure components.
These industry-specific examples highlight the indispensable role of SCADA systems in automating and optimizing industrial operations.
What are Smart Sensors and How are They Changing the Field of Instrumentation?
Smart sensors embody a transformative leap in the realm of instrumentation, merging sophisticated processing capabilities directly with traditional sensing mechanisms. These innovative sensors are distinguished by their dual ability to not only capture but also to process and disseminate data autonomously. Equipped with microprocessor technology, smart sensors can execute complex computations, perform self-diagnostics, and interface with other devices and networks independently, eliminating the need for external processing resources.
IoT Integration: Enhancing Connectivity and Data Collection
The Internet of Things (IoT) has revolutionized modern instrumentation by significantly enhancing connectivity and data collection. Through IoT integration, devices are empowered to communicate and exchange data over the internet, fostering a unified network of interconnected devices. This advanced connectivity not only enables the real-time analysis of data but also streamlines decision-making processes, elevating operational efficiency and adaptability.
The continuous monitoring of processes and environmental conditions, accessible from any location at any time, heralds a new era in instrumentation. It unlocks novel avenues for remote monitoring, control, and optimization of industrial operations, thereby broadening the horizons of what’s achievable in the realm of instrumentation.
Predictive Maintenance Capabilities: Reducing Downtime and Costs
The introduction of predictive maintenance capabilities, underpinned by smart sensors and IoT technology, marks a significant evolution in equipment and machinery management. This approach allows for the continuous monitoring of equipment conditions, enabling the anticipation of failures before they manifest. Such foresight facilitates timely maintenance interventions, averting unforeseen downtime and prolonging equipment lifespan.
The transition to predictive maintenance not only yields considerable cost savings but also bolsters operational reliability. By employing data analytics and machine learning algorithms, predictive maintenance systems can detect patterns and anomalies indicative of impending equipment failures. This delivers maintenance teams with actionable intelligence, empowering them to pre-empt costly malfunctions and optimize overall operational efficiency.
How do you Approach Troubleshooting a Malfunctioning Control System?
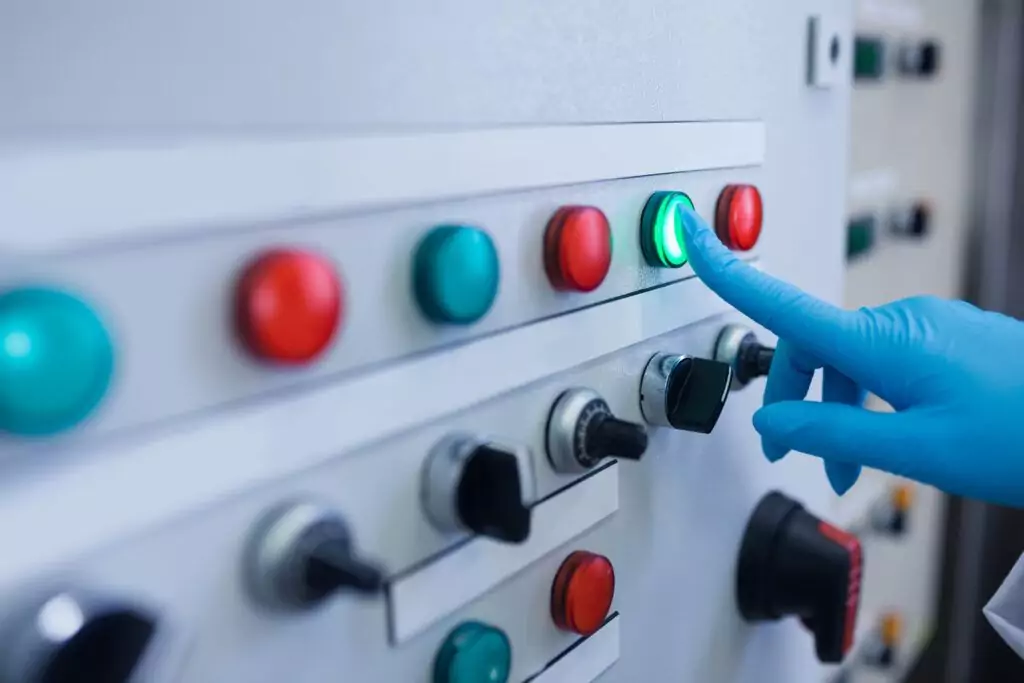
Troubleshooting a malfunctioning control system demands a systematic diagnostic process that sequentially moves from identifying symptoms to isolating the cause, and finally, to implementing a solution. The initial step hinges on gathering comprehensive information about the malfunction, including any error messages and the specific conditions under which the issue manifests. This stage often involves reviewing system logs and consulting with operators to piece together the events leading to the malfunction.
Systematic Diagnostic Process: Steps and Best Practices
Implementing a systematic diagnostic process is crucial for effectively troubleshooting and resolving malfunctions within control systems. The methodology unfolds as follows:
- Define the Problem: Begin with a comprehensive identification of the symptoms and the specific conditions under which the issue manifests. Utilize system logs, error messages, and operator feedback to gather detailed information.
- Isolate the Variables: Segment the system into manageable portions to pinpoint the problem area. This could involve dividing the system by functionality, components, or processes.
- Test and Analyze: Execute targeted testing on the isolated segments to detect any anomalies. Employ diagnostic tools and software for in-depth system performance analysis.
- Identify the Cause: Leverage the insights gained from testing and analysis to accurately determine the root cause, whether it relates to hardware, software, or procedural errors.
- Implement Solutions: Resolve the identified issue by repairing or replacing malfunctioning components, updating software, or modifying operational procedures.
- Verify and Monitor: Post-implementation, rigorously verify that the system operates as intended. Continue monitoring to ensure the problem does not reoccur.
Adhering to best practices, such as meticulous documentation of all investigative and corrective actions and leveraging multidisciplinary expertise, can significantly enhance the troubleshooting process.
Common Issues and Solutions: Examples in Pressure, Flow, and Temperature Control
Certain issues frequently emerge in the control of pressure, flow, and temperature within industrial systems, each necessitating specific solutions:
- Pressure Control:
- Issue: Oscillating pressure levels
- Solution: Inspect the system for leaks and evaluate pressure regulators for malfunctions, making adjustments or replacements as needed.
- Flow Control:
- Issue: Erratic flow rates
- Solution: Examine and cleanse any obstructed filters or valves. Confirm the operational integrity of pumps and motors.
- Temperature Control:
- Issue: Deviations in temperature readings
- Solution: Conduct calibration or replacement of compromised temperature sensors. Ensure heating or cooling units are functioning correctly.
For each category of control issue, employing a systematic diagnostic approach, from symptom identification through to the application of corrective measures, is essential for restoring system functionality and optimizing operational performance.
Explain the Importance of Calibration in Instrumentation
Calibration in instrumentation is a critical process that ensures the accuracy and reliability of measuring instruments and control systems. It involves the comparison of a device’s output under test to a known reference standard, with necessary adjustments made to align the device’s performance accurately with the reference. This process is vital for maintaining the integrity of data collected and the effectiveness of control systems across various sectors.
The significance of calibration lies in its impact on quality control, safety, and operational efficiency. Precise measurements are pivotal for maintaining consistent product quality, adhering to regulatory standards, and ensuring the safe operation of processes. Calibration aids in detecting inaccuracies and drift in instrument readings over time, which, if uncorrected, could lead to product quality issues, safety risks, or inefficient operations.
Accuracy and Reliability: Impact on Process Control
Accuracy and reliability are cornerstone principles in process control, pivotal for optimizing operational performance, ensuring product quality, and maintaining safety in industrial settings. Accuracy, the degree to which a measurement reflects the true value, is crucial for precise control actions that minimize variability in production processes. This precision directly influences product consistency, efficient use of resources, and waste reduction.
Reliability, on the other hand, ensures that instruments perform consistently over time, offering stability crucial for ongoing process control. The repercussions of inaccuracies or unreliability can be significant, potentially leading to unsafe operating conditions, process inefficiencies, and the risk of operational downtime. Regular calibration and maintenance are indispensable strategies for upholding these attributes, thereby securing the integrity and safety of industrial processes.
Calibration Standards and Procedures: ISO/IEC 17025 and Others
Calibration standards and procedures establish the foundational guidelines necessary for ensuring measurement accuracy and reliability. Among these, ISO/IEC 17025 is a globally recognized standard, delineating the general requirements for the competence of testing and calibration laboratories. Adherence to ISO/IEC 17025 demonstrates a laboratory’s ability to generate precise and dependable results.
Other critical standards include ANSI/NCSL Z540.1 and ISO 9001, which set forth criteria for calibration quality and management systems respectively. Compliance with these standards entails rigorous calibration procedures, encompassing the use of certified reference materials, the application of documented methodologies, and the traceability of measurements to national or international standards. By aligning with these established standards and procedures, organizations can significantly enhance the accuracy and reliability of their measuring instruments, thus bolstering the effectiveness and integrity of their process control systems.
What are the Latest Trends in Instrumentation & Control Engineering?
Instrumentation & Control Engineering is undergoing a dynamic transformation, propelled by technological advancements and the changing landscape of industrial requirements. At the forefront of these trends is the integration of Internet of Things (IoT) technologies, which is redefining the paradigms of device communication and operation within industrial frameworks. IoT facilitates real-time data collection and analysis, paving the way for predictive maintenance and process optimization.
Another pivotal trend is the adoption of wireless sensor networks (WSNs). These networks offer unprecedented flexibility, reduce installation costs, and enhance data acquisition capabilities, particularly in environments that pose logistical challenges. WSNs significantly boost system adaptability and scalability, aligning with the demands of contemporary industrial applications.
The incorporation of Artificial Intelligence (AI) and Machine Learning (ML) into control systems marks a revolutionary shift towards more intelligent automation and decision-making. AI and ML algorithms are capable of predicting system behaviours, optimizing operations, and improving fault detection mechanisms. This leads to heightened system reliability and operational efficiency.
In the current era, the emphasis on cybersecurity within control systems has become more pronounced. The growing connectivity and sophistication of modern instrumentation necessitate robust measures to shield critical infrastructure from cyber threats. This has led to the development of advanced communication protocols and systems designed to fortify cybersecurity.
Emerging technologies such as Augmented Reality (AR) and Virtual Reality (VR) are also starting to influence instrumentation and control engineering. These technologies offer novel approaches for training, system design, maintenance, and troubleshooting through immersive experiences that enhance comprehension and operational efficiency. In essence, the latest trends in instrumentation and control engineering are steering the field toward a future characterized by enhanced connectivity, intelligence, and security.
These developments hold the promise of elevating operational efficiency, safety, and sustainability across diverse industrial domains.
Wireless Sensor Networks: Applications and Benefits
Wireless Sensor Networks (WSNs) have emerged as a pivotal technology in instrumentation and control engineering, heralding a wide array of applications and benefits across diverse sectors. These networks comprise spatially distributed, autonomous sensors that monitor various physical or environmental conditions, ranging from temperature and sound to pressure and motion, and relay their data wirelessly to a central location. Key applications include:
- Industrial Automation: WSNs facilitate real-time monitoring and control over manufacturing processes, enhancing efficiency and safety.
- Environmental Monitoring: WSNs play a crucial role in observing environmental changes, contributing to conservation efforts and hazard detection.
- Healthcare: WSNs improve patient care through continuous monitoring and data collection, supporting timely medical interventions.
The advantages of WSNs are significant:
- Reduced Wiring Costs: The wireless nature of these networks slashes the need for extensive cabling, lowering installation expenses.
- Flexible Installation: WSNs can be deployed in hard-to-reach areas where traditional wiring is challenging or impossible.
- Scalability: Adding sensors to expand coverage or detail is straightforward, allowing for system growth with minimal hassle.
- Enhanced Operational Efficiency: Accurate, timely data from WSNs enable precise control actions, optimizing processes and outcomes.
- Energy Conservation: Low-power communication technologies ensure WSNs are energy-efficient and ideal for long-term use in remote locations.
Machine Learning and AI in Process Control: Predictive Analytics and Optimization
The integration of Machine Learning (ML) and Artificial Intelligence (AI) into process control is revolutionizing predictive analytics and optimization, marking a significant leap toward smarter industrial operations. By sifting through the extensive datasets generated by industrial processes, ML and AI algorithms unearth patterns and forecast future behaviours, a capability integral to:
- Predictive Maintenance: Identifying potential issues before they escalate, significantly curtailing downtime and maintenance costs.
- Process Optimization: Dynamically adjusting control parameters to maintain peak performance, thereby enhancing product quality and process efficiency.
- Quality Control: AI-driven anomaly detection ensures products meet stringent quality criteria.
Furthermore, ML and AI foster adaptive control strategies, where systems intelligently adjust to fluctuating process conditions in real-time, bolstering process resilience and efficiency. In essence, the application of ML and AI in process control heralds a future of more intelligent, efficient, and reliable industrial operations. Through predictive analytics and sophisticated optimization, industries stand to gain unparalleled levels of efficiency, quality, and sustainability.
Driving Innovation Through Precision and Control
From PID tuning and SCADA systems to smart sensors and predictive analytics, we’ve explored the key concepts, technologies, and strategies that define modern Instrumentation & Control Engineering. Whether you’re preparing for your next interview or refining your professional skills, understanding these core areas sets the stage for success in a rapidly evolving industry.
At Vista Projects, we harness decades of experience to deliver integrated engineeringThe process of integrated engineering involves multiple engineering disciplines working in conjunction with other project disciplines to e... solutions—including I&C systems—that are accurate, resilient, and built for the future. Our work empowers industries to operate smarter, safer, and more sustainable.
Inspired to advance your career in control systems? Explore opportunities with Vista Projects and help shape the future of intelligent industrial engineering.