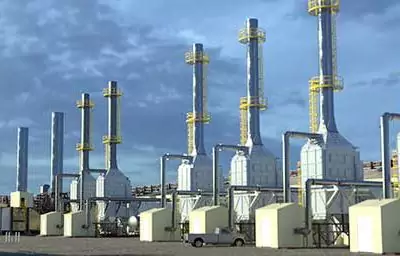
Enhanced Modified Vapour Extraction (eM-VAPEX) Recovery
Overview
Vista’s integrated engineering services on this project included the front-end engineering design (FEED) and detailed engineering (DE). The project called for enhanced modified vapour extraction (eM-VAPEX or emvapex) recovery technology at a steam-assisted gravity drainage (SAGD) processing facility. The installed eM-VAPEX technology included new facilities to process solvent for recovery and recompression. The project included 13 injector wells, which generated production from 24 existing producer wells.
Client
MEG Energy
Project/Facility
eM-VAPEX is a new solvent-based in-situ recovery technology that the client was implementing at a commercial SAGD facility.
Situation
eM-VAPEX has been shown to reduce water use and increase well performance. The client needed a trustworthy engineering partner with experience in integrating complex new technology.
Solution
Vista provided FEED and DE for this pilot project. The result was the deployment of an innovative heavy oil recovery technology at multiple well pads. The technology uses a solvent vapor delivered into typical injection wells from the beginning of the reservoir lifecycle.
Vista’s engineering design allowed the client to efficiently strip out the solvent from the production stream at the well pad. The solvent was then recompressed and returned back to the reservoir.
The results from the pilot facility indicate increased bitumen rates and a lower cumulative steam-to-oil ratio. This resulted in reduced water usage as well as lower costs and greenhouse gas (GHG) emissions.
The client has been pleased with the engineering results. They are now awaiting appropriate market conditions to expand its use of the eM-VAPEX recovery technology.
Success Factors
Having worked with the client for several years, Vista attributes the success of its ongoing relationship to several factors. Most importantly, Vista was able to establish a dedicated team who shared a long-term vision with the client. We took a collaborative approach to perfect the design and reduce engineering costs.
Additional success factors included:
- Flexibility of Vista’s engineering team and balancing resources across multiple projects
- Direct award with Vista/owner alignment on project drivers
- Modularization optimization
- Standardized equipment selection
- Cost/schedule certainty based on Vista’s wealth of experience in the oil sands and heavy oil
eM-VAPEX Equipment & Technology
The eM-VAPEX design included the installation of a solvent storage bullet, loading facilities, and injection pumps. It also included all the solvent recovery equipment needed to make the process self-sustaining with very little make-up solvent.
Related eM-VAPEX Engineering Applications
The engineering capabilities Vista demonstrated on this eM-VAPEX project apply to multiple markets. In particular, companies that need support in the heavy oil and natural gas processing industrial spaces will benefit from our experience.